Más leído
- 1. Yolanda Díaz, ministra de Trabajo y Economía Social, visita Copreci
- 2. El Grupo MSI recibe el premio a la mejor pyme industrial del año
- 3. 20 años de cooperativismo y mucho corazón
- 4. Nueva edición del Foro de Personas de MONDRAGON
- 5. LagunAro concluye con nota 2024 y afronta con solidez sus retos de futuro
- 6. Fagor Arrasate suministra líneas de corte de acero a la mexicana Ternium
MSI Grupo desarrolla la instalación del transporte automático en Mercedes Benz Vitoria
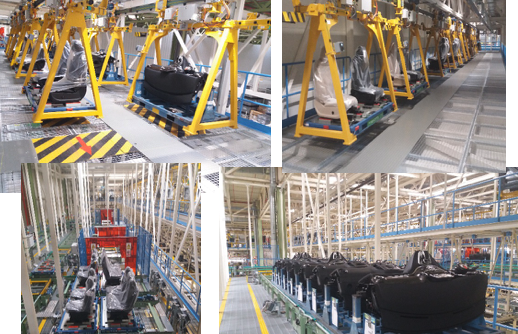
Una de las finalidades del proyecto es reducir el tráfico dentro de la nave de Montaje Final de la fábrica, originado en gran parte por el flujo logístico de estos componentes (cockpit y asientos) al trasladarse desde el I-Park hasta la cadena de montaje final.
El I-Park se une a la nave de montaje final a través de un túnel suspendido, dentro del cual se ha instalado una electro vía de más de 1km. Los productos que se pre-montan en el I-Park en skids que son cargados por robot en los conveyor. A continuación a través de elevadores son llevados a las perchas de la electro vía para su transporte y descarga en la línea de montaje final. Todo ello manteniendo la secuencia prevista en producción, reduciendo los tiempos de tránsito y mejorando la calidad de transporte en la recogida, tránsito y entrega de los diferentes elementos.
El proyecto abarca el suministro de los productos de los siguientes proveedores:
- SAS Automotive (Cockpit)
- FAURECIA (Asientos delanteros)
- LEAR (Asientos traseros)
DESCRIPCIÓN DEL SISTEMA
Los elementos que componen la nueva instalación de transporte automático son:
- Sistema de transporte aéreo mediante 1.250 metros de electrovía y 86 perchas de carga de productos que comunica cada instalación de los proveedores en el I-Park con la nave de Montaje Final de Mercedes:
- 514 metros de línea aérea de electrovía en I-Park en cota 6 m.
- 3 Descensores y 3 Elevadores de electrovía en I-Park entre las zonas de carga/descarga de proveedores en cota 0m. y la línea aérea en cota 6m.
- 2 Cambios de vía convergentes y 2 cambios de vía divergentes en la línea aérea del I-Park.
- 110 metros de línea aérea de electrovía en túnel de comunicación entre I-Park y nave de Montaje Final en cota 6 m.
- 478 metros de línea aérea de electrovía en “mochila” adyacente a nave de Montaje Final en cota 6 m.
- 148 metros de línea aérea de electrovía en nave de Montaje Final en cota 6 m
- 3 Cambios de vía divergentes y 2 cambios de vía convergentes en línea aérea de la nave de Montaje Final.
- 2 Descensores y 2 Elevadores de horquillas en nave de Montaje Final para intercambio de producto entre la electrovía en cota 6m. y el sistema de manutención de mesas de cadenas cota 3,8m.
- 10 Antenas RFID para identificación y gestión del suministro de productos.
- Sistema de transporte y distribución de productos y entrega en línea en nave de Montaje Final mediante 436 metros de manutención de mesas de cadena en cota 3,80m y 0m para la distribución de productos a los puntos de montaje en las líneas 2 y 5:
- 76 Mesas de transporte de cadenas.
- 27 Mesas de transporte de cadenas transversales.
- 39 Mesas de transporte de cadenas excéntricas.
- 13 Mesas de cadenas de acumulo.
- 4 Mesas tijera.
- 4 Mesas de giro a 90º y 180º
- 5 Elevadores/Descensores de cadenas para intercambio de producto entre la cota 3,8m y la cota 0m de entrega en línea de montaje.
- 14 Antenas RFID para identificación y gestión del suministro de productos.
- Sistema de control:
- 3 Armarios principales de zona.
- 8 Armarios de control periféricos.
- 39 Pupitres locales de mando equipados con panales de operador táctiles TP1200 de Siemens.
- 45 Key Panel Profinet Siemens KP32F
- 9 Key Panel Profinet Siemens KP8F
- 4 PLCs Siemens S7-300 con CPU 319F3-PN/DP y módulo Ethernet CP343-1.
- 28 Equipos de periferia descentralizada ETS200 en Profinet.
- 219 Drives Siemens G120D