División de máquina herramienta de la Corporación MONDRAGON
Diseño y fabricación de prensas y sistemas de estampación, laminado, procesado y corte de metales y soluciones en conformación de chapa.
Más leído
- 1. Nueva edición del Foro de Personas de MONDRAGON
- 2. LagunAro concluye con nota 2024 y afronta con solidez sus retos de futuro
- 3. Fagor Arrasate suministra líneas de corte de acero a la mexicana Ternium
- 4. Los retos de futuro de LagunAro, en el último número de la revista TU Lankide
- 5. Danobatgroup marca un nuevo récord de facturación en 2024 con 344 M€
- 6. Reconocimiento al liderazgo de las mujeres cooperativistas en el 8M
Danobatgroup y Fagor Arrasate desarrollan una línea de corte de chapa con tecnología láser blanking
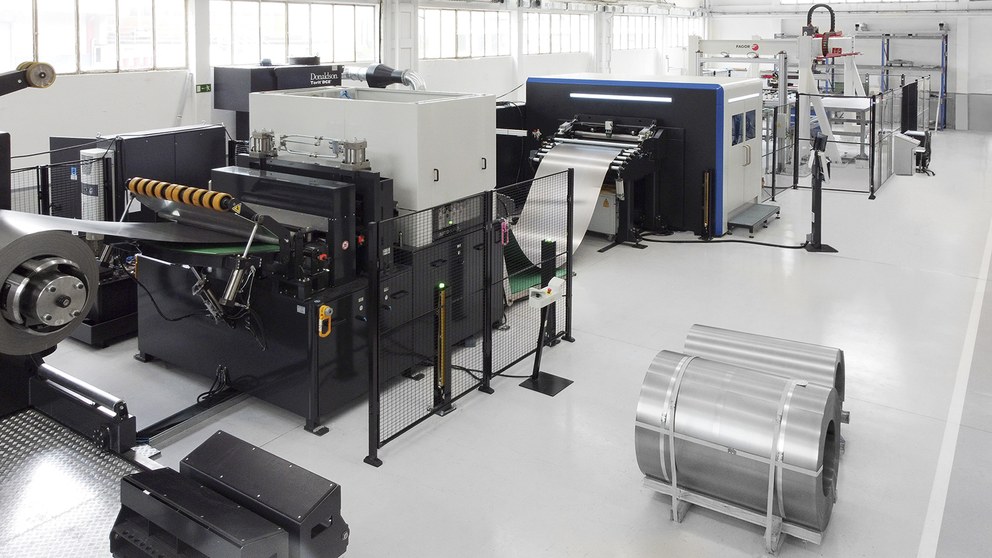
El fabricante de máquina herramienta Danobatgroup, a través de su unidad de negocio de trasformación de chapa, y el líder mundial en el desarrollo de soluciones de conformado de acero Fagor Arrasate han diseñado y fabricado una solución pionera de corte de chapa a partir de bobina metálica para su uso en sectores estratégicos para la economía como la automoción.
La solución, conocida como láser blanking, supone una innovadora alternativa al tradicional corte por prensa y es fruto de una alianza colaborativa que ha permitido a Danobatgroup y a Fagor Arrasate, integradas en la Corporación MONDRAGON, impulsar la transferencia tecnológica entre ambas empresas y crear una solución tecnológicamente puntera, robusta y competitiva.
Se trata de un desarrollo que proyecta al sector de la máquina herramienta en el exterior y refuerza el posicionamiento internacional del tejido industrial vasco.
Su principal ventaja competitiva, respecto a los sistemas utilizados hasta ahora, es que reduce los tiempos de preparación respecto a prensa blanking, ofrece más flexibilidad para cambios, y elimina el uso de troquel; y respecto a un láser convencional ofrece mayor productividad y una mejor calidad de corte. El desarrollo combina diferentes tecnologías para hacerse cargo del proceso completo de forma automatizada, por lo que el material procedente de la bobina es aplanado, cortado y finalmente apilado.
La máquina, que puede integrar varios cabezales de corte láser, tiene capacidad para trabajar con diferentes materiales como acero común, inoxidable, aceros de alta resistencia HSS o aluminio, en anchos, espesores y calidades diferentes.
Este desarrollo está dirigido a los fabricantes de automóviles (OEMS), los proveedores de componentes de automoción (TIER1) y los centros de servicio que suministran chapa cortada en formatos a diferentes empresas industriales.

En el ámbito de la automoción, esta solución es especialmente útil para la fabricación de series de vehículos cortas o limitadas, gamas especiales, vehículos eléctricos y para los fabricantes de repuestos y carrocería.
También puede tener aplicaciones en el prototipado, porque la flexibilidad de este sistema permite hacer cambios de diseño sin la necesidad del uso de troqueles.
“Al ser una línea flexible se puede adaptar a diferentes anchos de medida y distribuir por toda la superficie de la chapa el dibujo de las piezas que hay fabricar, aprovechando mucho mejor el material. Esta distribución óptima de las piezas en la banda desemboca en un ahorro de material de hasta un 10%. Este porcentaje es muy relevante ya que el material supone el 80% de los costes”, asegura el director comercial de la Unidad de Negocio de Siderurgia de Fagor Arrasate, Mikel López.
Otro beneficio importante es que, al no precisar de troqueles, la producción no se detiene ya que las distintas geometrías de piezas están preprogramadas y el cambio de producción es casi inmediato. Además, se ahorra espacio en planta porque las áreas de almacenamiento para los diferentes conjuntos de troqueles ya no son necesarias.
El valor de la intercooperación
Para el diseño y fabricación de esta solución ha sido necesaria la suma de capacidades de dos empresas líderes en sus ámbitos de actividad.
Danobatgroup ha aportado su conocimiento en el desarrollo de soluciones de corte láser y su capacidad en el desarrollo de softwares de simulación. Mientras que Fagor Arrasate ha sumado su conocimiento en el procesado de materiales y de las necesidades y exigencias del sector del automóvil.
Aseguran desde ambas empresas que la intercooperación de “dos compañías hermanas y complementarias ha hecho posible desarrollar un producto que combina las competencias de cada una para ofrecer al mercado una solución innovadora y generar valor”.