Most read
- 1. Danobatgroup sets a new turnover record of €344 M in 2024
- 2. Danobat revolutionizes manufacturing with a new precision robot
- 3. MONDRAGON expands its digital presence with Bluesky
- 4. MONDRAGON leads ASETT, the Social Economy Hub for social transformation
- 5. Orbik Cybersecurity, the first technological start-up to become a co-operative
- 6. Eika acquires Stone Cooker S.L and its innovative 'Suiseki' table to boost growth
High-precision Danobat-Overbeck grinding machine for machining spindles and tool holders
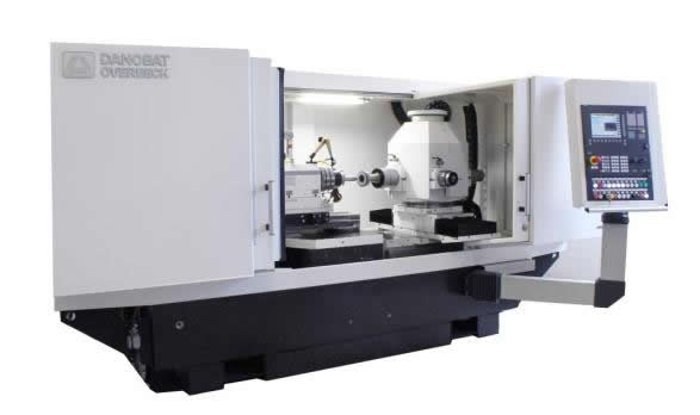
This grinding machine, designed in Herborn (Germany), can be used on workpieces with a maximum length of 1,300 mm (with a longitudinal OD/ID of 280 mm). Grinding diameters of 400 mm on workpieces weighing as much as 350 kg is also possible.
With a long-standing track record of over 90 years in developing internal and external cylindrical grinders to the highest quality standards, the brand has exploited its expertise to design this new equipment with perfect vibration damping and excellent thermal stability thanks to its natural granite bench and cooling system for the workhead and X and Z axes.
In addition, the device offers high accuracy thanks to the linear motor technology on the X and Z axes as well as maximum static and dynamic stability through amply dimensioned slide units with linear motion roller guides.
Positioning on the grinding machine is by means of absolute linear scales, direct drive workhead spindle (C0 axis) with preloaded precision bearings and variable speed adjustment from 0-1,000 rpm. The machine is also equipped with a high precision swivelling workhead (B-axis), a rotary spindle turret for greater versatility with an option to integrate up to 4 spindles, a direct drive torque motor and a measuring system with a high-resolution encoder of 0.0001°.
A Siemens Sinumerik 840D SL with Safety Integrated CNC unit and Windows-based software for quick and easy reference change are used.
Another feature of the ID-400 L is its highly modular design, which enables every customer to configure a machine that meets his individual needs: a variety of grinding spindles, diamond-dresser configurations, workpiece clamping systems and several options for measuring tools and customisation of measuring cycles among other possibilities.
Collaboration with Seco EPB
Recently, DANOBAT-OVERBECK has collaborated with the French firm Seco EPB, one of the leading manufacturers of cutting tools and tool holders internationally.
The French company produces high precision equipment such as the HSK toolholder on a Danobat-Overbeck ID-400 L grinding machine, but this model is also conceived for non-cylindrical grinding operations so that other applications made by Seco such as the Capto model can also be produced with ease.
For non-cylindrical grinding purposes, the work spindle (C0-axis) is equipped with a high-resolution rotary encoder, which permits 3-axes interpolation of the C0, X and Z axes.
The ID-400 L is also equipped with a W-axis mounted on an extremely rigid swivel unit which allows the machining of long shaft workpieces using steady rests made by Danobat.
This equipment is also particularly suitable for taper grinding because the B0-axis can be swivelled making it possible to grind different taper angles with a standard cylindrical grinding wheel without any need for a profiled tapered grinding wheel.