Most read
- 1. Danobatgroup sets a new turnover record of €344 M in 2024
- 2. Danobat revolutionizes manufacturing with a new precision robot
- 3. MONDRAGON expands its digital presence with Bluesky
- 4. MONDRAGON leads ASETT, the Social Economy Hub for social transformation
- 5. Orbik Cybersecurity, the first technological start-up to become a co-operative
- 6. Eika acquires Stone Cooker S.L and its innovative 'Suiseki' table to boost growth
Detecting failures before they occur
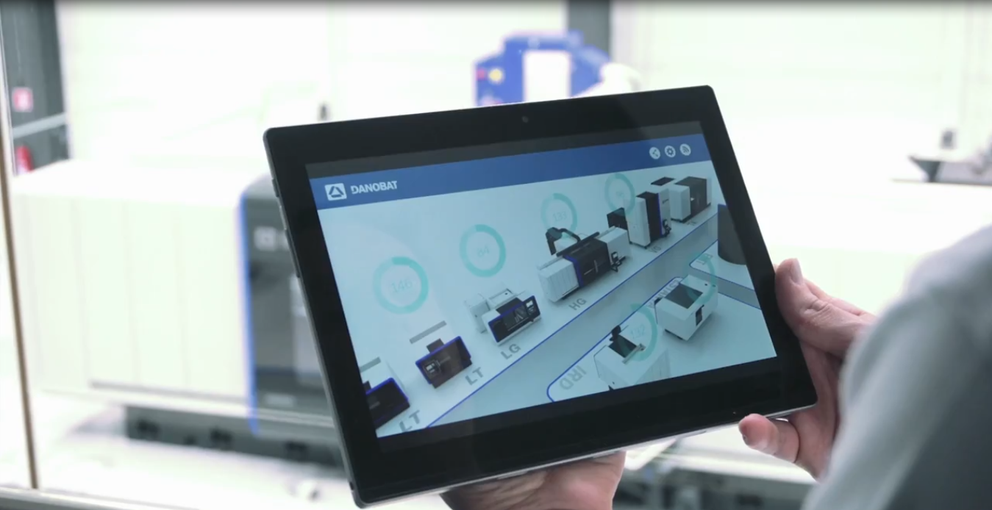
Avoiding breakdowns and production stops, increasing the availability of equipment and ensuring optimum performance are some of the main concerns of companies that use machine tools to manufacture industrial parts and components of high added value with ultra-precision results.
It is in this context that the European project PreCoM (Predictive Cognitive Maintenance Decision Support System)is being developed, an initiative that has the participation of the Basque technology center IK4-IDEKO and pursues the objective of developing an intelligent platform for the capture and analysis of data from machines, to optimize the maintenance tasks of the equipment. The platform will be a support system for a predictive cognitive maintenance decision-support system able to identify and localize damage, assess damage severity, predict damage evolution, assess remaining asset life, reduce the probability of false alarms, provide more accurate failure detection, and issue notices to activate preventive maintenance actions.
"Ultimately, the developed platform is an intelligent system that increases the in-service efficiency of the equipment by at least 10%," says Iñigo Bediaga, the person responsible for the project at the IK4-IDEKO research center. The PreCoM initiative, which started at the end of 2017 and will continue until 2020, has also set goals such as increasing the availability of equipment, reducing incidents related to machine failures, reducing energy consumption and the reduction of raw material consumption.
The project consortium, led by the Swedish university Linneaus University, is made up of 17 international partners among which, in addition to IK4-IDEKO, are the machine tool manufacturers SORALUCE and DANOBAT Overbeck and a company specializing in the development of monitoring systems and big data analysis in manufacturing industry, SAVVY.
The consortium includes 3 end-user factories, 3 machine-tool suppliers, 1 leading component supplier, 4 innovative SMEs, 3 research organizations and 3 academic institutions. Together, we will validate the platform in a broad spectrum of real-life industrial scenarios (low volume, high volume and continuous manufacturing). We will also demonstrate the direct impact of the platform on maintainability, availability, work safety and costs in order to document the results in detailed business cases for widespread industry dissemination and exploitation. The project has a duration of 3 years and an EC requested contribution of €6.1M
Sensor solutions/Sensing to anticipate breakdowns
The PreCOM consortium will be responsible for developing and validating a cognitive predictive maintenance decision support system composed of four differentiated modules. The first of these modules is designed for the acquisition of data through the use of both external sensors and sensors embedded into the components of the machine-tool, with the mission of providing information that makes possible the detection of anomalous behavior.
"The current development of Cheaper and more powerful sensors, together with big data analytics, gives us a unique opportunity to carry out an exhaustive and precise monitoring of the state of the machine tool," says the researcher.